广麟材耀开辟锂电池封装材料领域新赛道
大力创新研发,抢占铝塑膜国产化高地
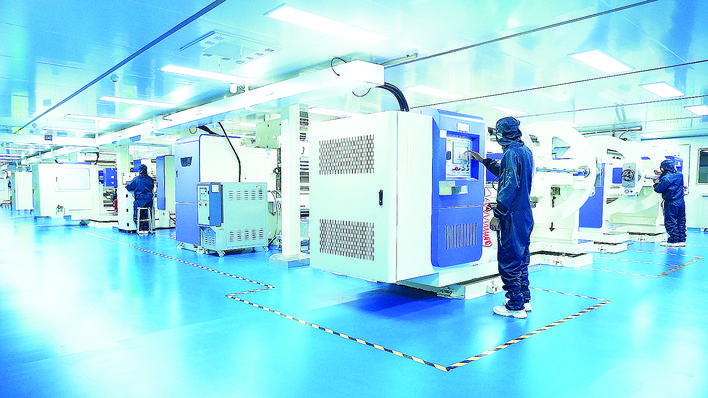
广麟材耀自动化生产车间。惠州日报记者钟畅新 通讯员何雅怡 摄
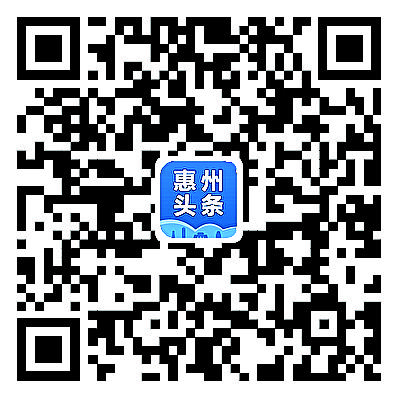
扫码看视频
宽敞、整洁、明亮的车间里,每台大机器都在快速运转,从基材放卷到最后收卷出品铝塑膜,一台机器只需两三个人操作,基本实现了全程自动化……这里是广东广麟材耀新能源材料有限公司(以下简称“广麟材耀”)的生产车间。
目前,惠州正大力推动新型储能产业高质量发展,而铝塑膜则是锂电池材料国产化的最后一块高地。近年来,广麟材耀面向锂电池封装材料领域开辟新赛道,在国内率先实现关键核心材料完全自主研发,产品性能及一致性已达行业领先水平,出货量位居行业前三,成为3C数码产品、储能及动力电池领域“国产替代进口”征程上的先行者。
多次研发迭代,创新工艺实现个性化定制
铝塑膜,对普通人来说或许有些陌生,它其实离我们很近。在我们每天使用的手机里,都有一层不到0.1毫米厚的铝塑膜包裹着手机外壳下的电池。电动汽车里的电池外也可能包裹着这层膜。
这层看似不起眼的银色薄膜,却是锂电池中生产技术难度最大的材料之一。
“铝塑膜是一种软包锂离子电池的封装材料,对锂离子电池内部能起到良好的保护作用。”广麟材耀总经理刘德胜介绍,相较于钢壳或铝壳封装方式,使用铝塑膜的软包封装具有安全性能高、重量轻、厚度薄、能量密度高等优点。
广麟材耀成立于2000年,前期主要以涂布、复合技术和高分子材料为依托,专注于静电防护材料的研发及生产。2012年起,基于多年积累的经验,并汲取日本先进的生产制造工艺技术,广麟材耀启动了锂电池铝塑膜项目。
新的领域意味着新的起点。为取得铝塑膜进口替代从“0”到“1”的突破,广麟材耀在研发上倾注了更多人力物力。同年,公司成立专门从事铝塑膜材料研究的科学院。总经理刘德胜还多次到日本学习及引进相关技术、设备,保证广麟材耀在业内具有一定竞争力。
功夫不负有心人。经过多次研发迭代,2015年,广麟材耀实现了自主生产铝塑膜的目标。“相较于国外生产的铝塑膜,我们可以根据客户的需求量身定制,主要体现在调整产品的层间结构、宽幅等,以至于适配性更优。”刘德胜说。
自主研发原材料,从源头上杜绝卡脖子
过去,铝塑膜市场长期被日韩企业占据绝大部分份额,核心技术也都掌握在这些国家手中。
刘德胜介绍,生产铝塑膜所需的原材料,大部分在国内有企业可自主供应,铝箔、尼龙、PP等都可以在国内找到成熟的供应商,唯独其中用于涂布、复合的胶粘剂,原来一直掌握在外国人手中。
“最开始,我们生产铝塑膜时所用的胶粘剂都需要从国外进口,他们每个月给我们供应5万吨。当我们扩大产能,需求量达25万吨的时候,人家就死死卡住,怎么都不愿意给了。”刘德胜说,有了被“卡脖子”的经历后,广麟材耀才如梦初醒——实现进口替代迫在眉睫。
为了打破原材料、工艺方面的壁垒,持续的研发投入是广麟材耀团队取得突破的核心。该公司围绕产品性能持续发力,在研发方面的固定资产超2000万元,研发人员占比超过15%,已获得近40项专利成果。
经过自主研发,目前,广麟材耀除铝箔、尼龙两类由国内工艺已成熟的公司提供原材料外,其余核心原材料完全实现自主供应。正因如此,即使2019年日本对国内原材料出口收紧时,广麟材耀仍能持续保证供应。
从原材料上突破“卡脖子”难题,也帮助广麟材耀进一步实现了降本增效。根据数据统计,目前广麟材耀在保证产品性能的基础上,已实现材料成本低于行业平均水平20%。
就这样,广麟材耀率先成为国内首家关键核心材料完全自主的铝塑膜企业。在此基础上,该公司的“国产化”铝塑膜近年来已一点一点“蚕食”原本掌握在日韩手里的铝塑膜市场。目前广麟材耀已研发出20多款产品,2处厂区8条产线的年总产能约1亿平方米,市场占有率排名全国前三。其中,纯正干法、纯正热法总产能达1500万平方米/月。
“随着产能扩大,我们还计划走上市融资之路,促进企业进一步快速发展,因此公司总部搬迁势在必行。”刘德胜说,去年他曾在珠三角多个城市“找了一大圈”,磨破了两双鞋,最终选择将公司总部从深圳市南山区迁至惠州,并于去年8月完成搬迁。
“惠州是我们的风水宝地,这里不仅有新型储能产业链的优势,而且投资环境也非常适宜中小型生产企业,在这里,我们有信心得到更快速的发展。”展望前景,刘德胜说,广麟材耀目前已在做前期准备工作,预计2024年上半年申报科创板IPO,力争成为更具竞争力的锂电池铝塑膜制造商。
惠州日报记者游璇钰 陈相成 实习生翁玮
- 上一篇:惠河高速改扩建项目开启路面施工
- 下一篇:海关总署:今起入境人员无需核酸或抗原检测